Opera
Galleria Olimpia
Cliente
Aspi (Autostrade per l’Italia Spa)
Fornitura
Tre carri porta forme Volto con sistema MR4.0
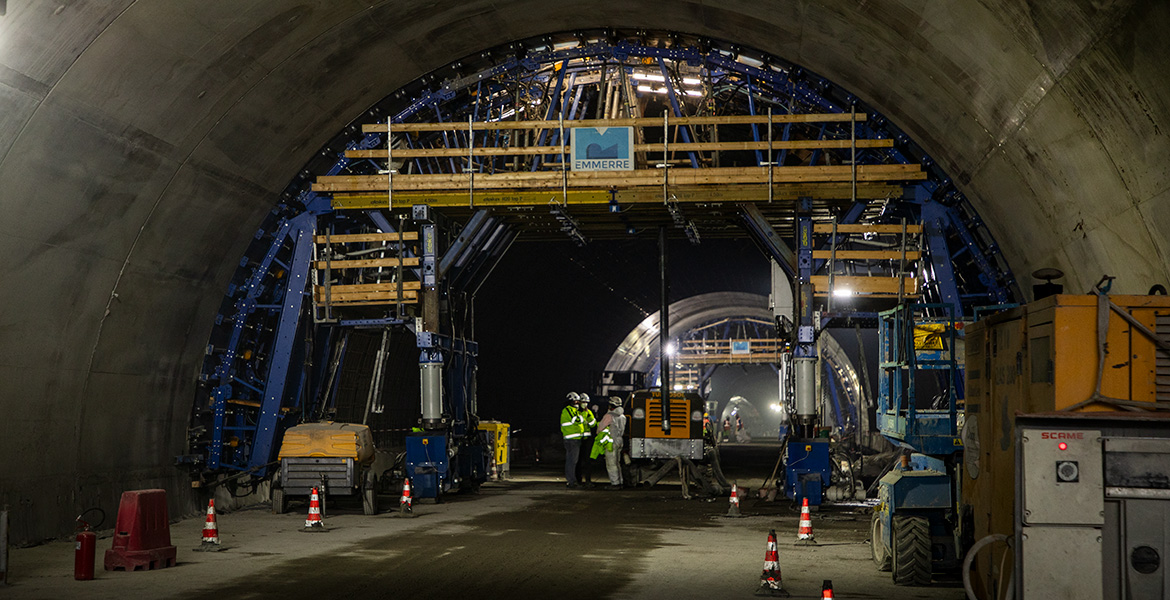
Sicurezza first
Traffico, condizioni meteo avverse, scarsi spazi di lavoro a disposizione, tempi di cantiere esigenti, necessità di tutelare al massimo la sicurezza dei lavoratori e, infine (ma perché farsi mancare qualcosa) gli insulti degli automobilisti, inferociti per le inevitabili ripercussioni sulle loro esigenze di spostamento.
Stiamo parlando di uno degli incubi peggiori di ogni impresa di costruzioni: la riqualificazione radicale di una galleria autostradale.
Questa sorta di inferno logistico si porta dietro un’ulteriore problematica, in grado di creare se non prevista in fase di pianificazione e rilievo ulteriori ritardi e livelli di complessità; stiamo parlando di una riqualificazione e, quindi, di un intervento che viene a innestarsi su un manufatto esistente, che, ricordiamolo, si sviluppa quindi in sotterranea con gradi di incertezza sulle caratteristiche tecniche di materiali e soluzioni progettuali utilizzate nel passato che non sempre si possono prevedere con sondaggi e analisi preliminari.
Proprio su uno di questi cantieri, vi portiamo oggi, per vedere al lavoro tre carri di getto di EMMERRE noleggiati da Amplia per il rifacimento delle volte della galleria Olimpia, che si sviluppa lungo l’Autostrada A26 (“dei Trafori” giusto per capire quante gallerie prevede), tra Alessandria Sud e quello di Casale Monferrato Sud.
Prima però di entrare nel dettaglio dell’opera, è necessario effettuare un inquadramento generale della stessa all’interno del piano di manutenzione che Aspi (acronimo di Autostrade per l’Italia Spa, tornata di proprietà pubblica nel 2022) sta realizzando sulla rete gestita.
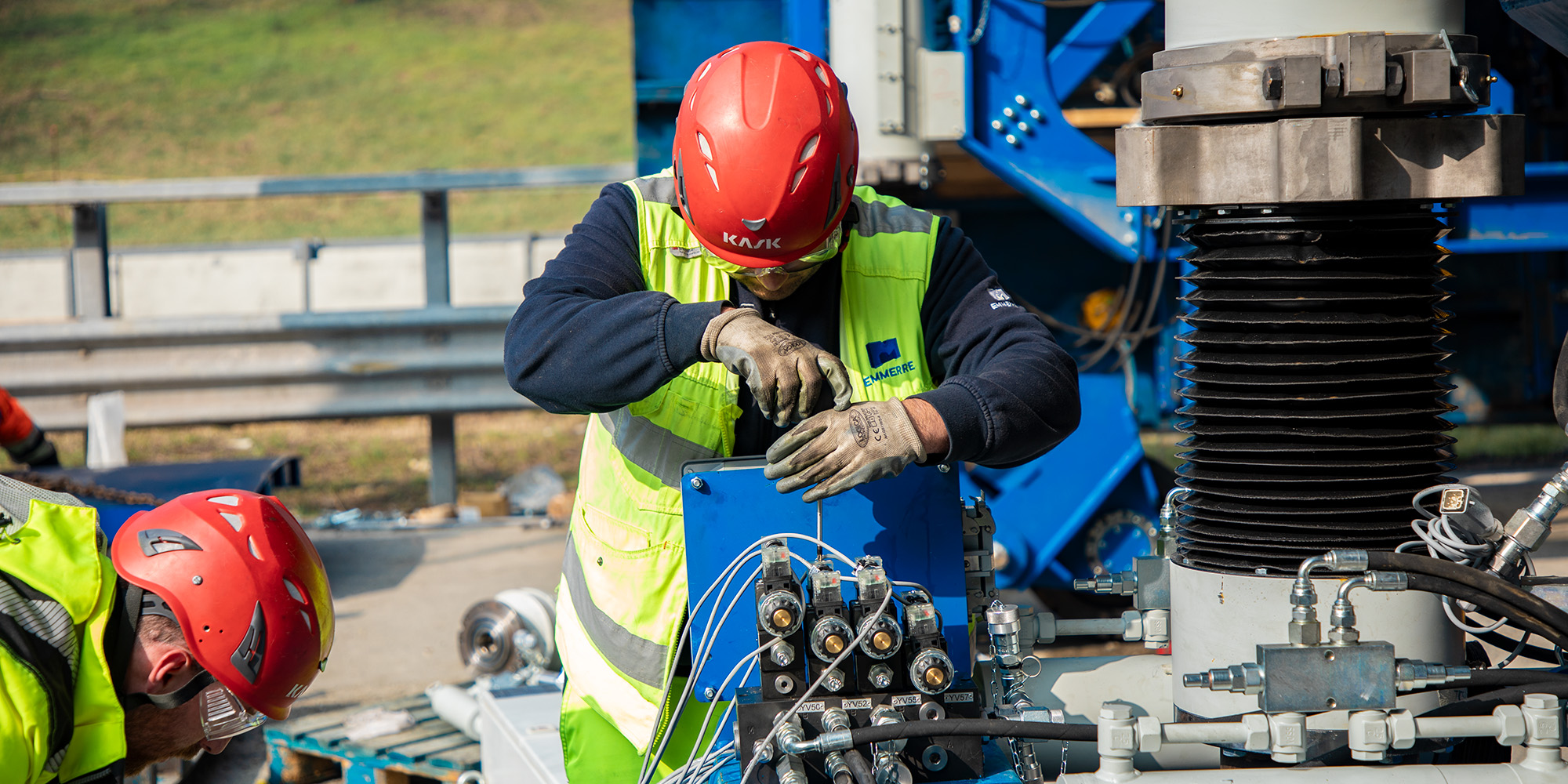
Proprio su uno di questi cantieri, vi portiamo oggi, per vedere al lavoro tre carri di getto di EMMERRE noleggiati da Amplia per il rifacimento delle volte della galleria Olimpia, che si sviluppa lungo l’Autostrada A26 (“dei Trafori” giusto per capire quante gallerie prevede), tra Alessandria Sud e quello di Casale Monferrato Sud.
Prima però di entrare nel dettaglio dell’opera, è necessario effettuare un inquadramento generale della stessa all’interno del piano di manutenzione che Aspi (acronimo di Autostrade per l’Italia Spa, tornata di proprietà pubblica nel 2022) sta realizzando sulla rete gestita.
Una visione complessiva
Un piano che definire imponente sarebbe probabilmente riduttivo, non solo per i valori economici in gioco, ma anche per la complessità di interventi da realizzare che, come dicevamo, spesso riguardano riqualificazioni della rete in presenza di traffico o potenziamenti in aree particolarmente complesse da gestire non solo dal punto di vista logistico, ma anche tecnologico.
Qualche numero quindi? Lo scorso anno Aspi ha messo in campo un investimento di oltre 1,6 miliardi di euro per seguire più di 110.000 interventi sia per attività di manutenzione sia per interventi di realizzazione di nuove infrastrutture fondamentali per dare risposta alle aumentate esigenze di traffico di numerose tratte autostradali del nostro Paese.
Per chi fosse interessato ad andare più in profondità: del totale, circa 500 milioni sono stati spesi per la manutenzione ordinaria della rete, ben 700 per gli ammodernamenti (e quindi anche per interventi come quelli della galleria Olimpia) e circa 400 per realizzare nuove opere.
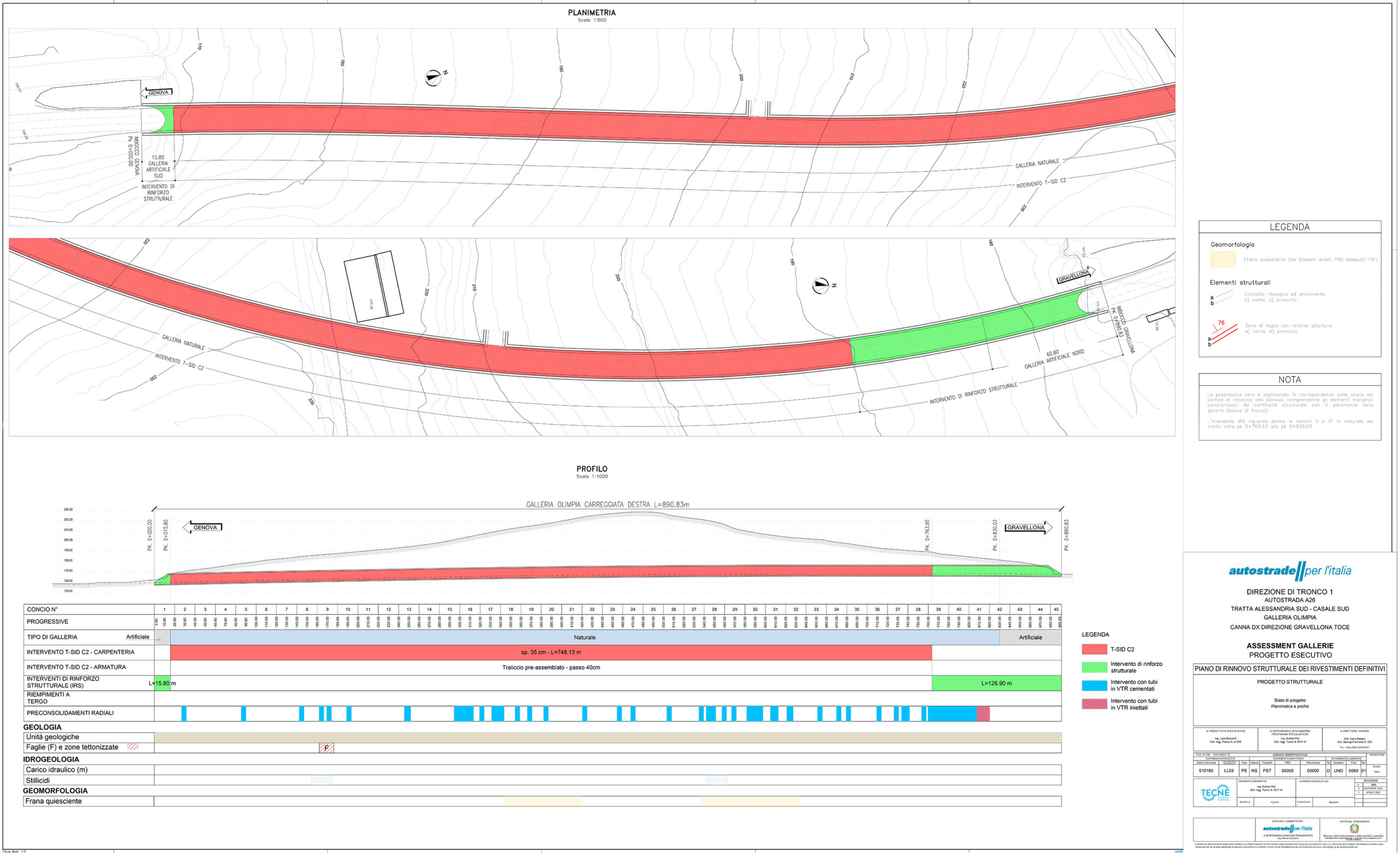
Anche il 2024 prosegue sulla stessa linea, con circa 1,4 miliardi di investimenti previsti a cui si sommano altri 400 milioni per il piano di manutenzione annuale.
Il piano di ammodernamento viene svolto con il concorso di tutte le principali società del gruppo Autostrade per l’Italia: gli interventi vengono progettati dalla società di ingegneria Tecne ed eseguiti, secondo quanto previsto dalla normativa, da Amplia.
Il polo tecnologico Muovy è dedicato allo sviluppo delle soluzioni digitali a disposizione del Gruppo e ha elaborato il calcolo del rimborso sulla base di dati proprietari di ASPI.
50 anni nel futuro
Parlando esclusivamente del piano di ammodernamento, di cui la galleria Olimpia fa parte e che impatta molto sullle gallerie liguri e piemontesi rappresentano una parte estremamente importante del totale nazionale, dato che, solo in Liguria ci sono 285 gallerie (il 48% del totale a livello nazionale ASPI), e 516 ponti e viadotti.
L’obiettivo del piano in corso – che proseguirà nei prossimi anni – è quello di rinnovare il ciclo di vita dei manufatti che insistono sulla rete, mettendo in campo un investimento complessivo di oltre 21,5 miliardi tra investimenti e manutenzioni previsti nel piano industriale per lo sviluppo della rete e ammodernando infrastrutture realizzate negli anni ’60/’70.
Ora possiamo entrare nel dettaglio dell’intervento di ammodernamento della galleria Olimpia, canna nord, progettato da Tecne e in corso di realizzazione da pare di Amplia, società entrambe del gruppo Autostrade per l’Italia.
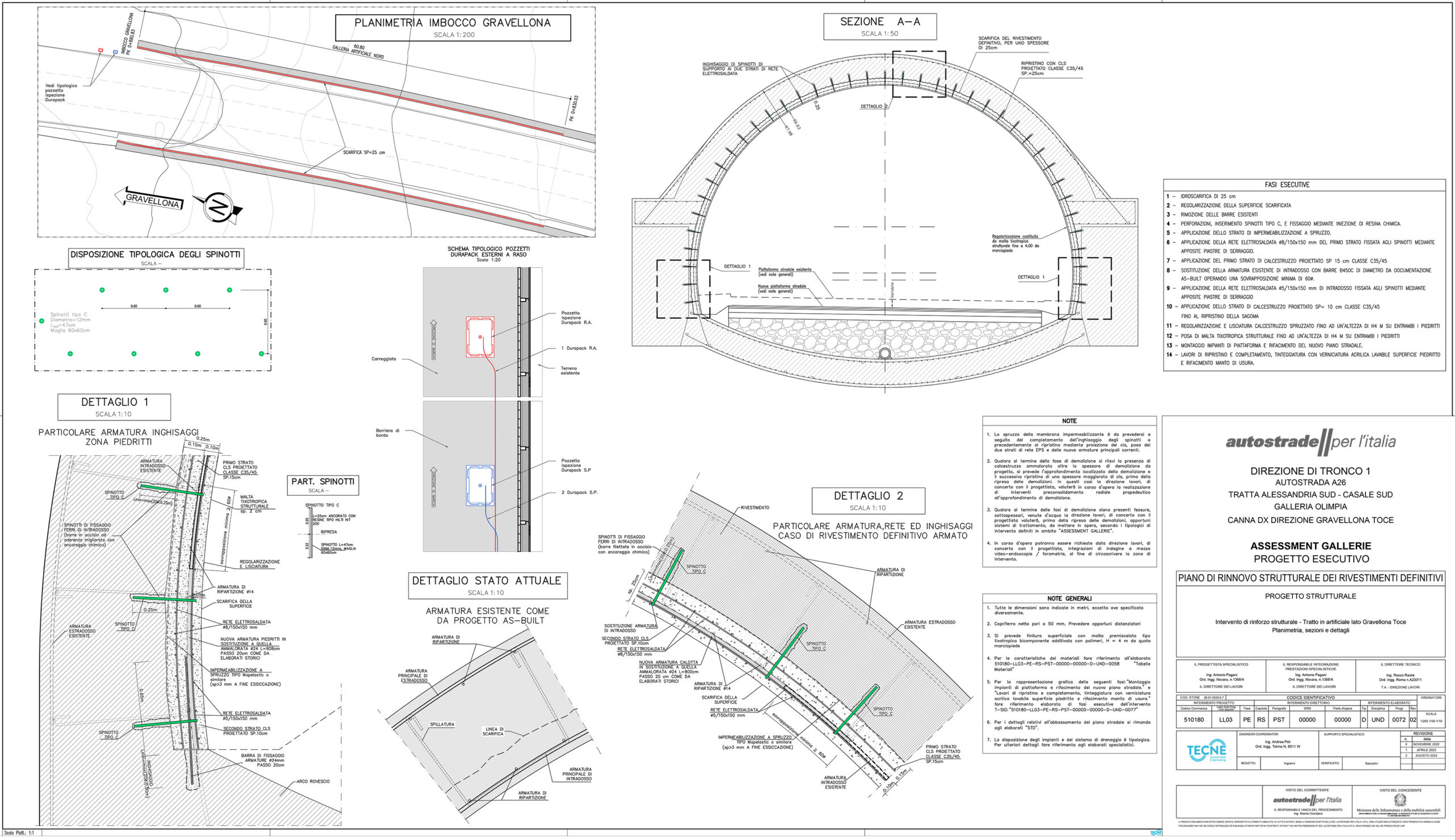
Sul cantiere, invitati da Emmerre che ha fornito i casseri per il getto delle volte, ci riceve, Enrico Onniboni, direttore di cantiere per Amplia Infrastructures che ci spiega l’operatività in dettaglio: “La galleria Olimpia, all’interno del piano di riqualificazione delle gallerie voluto dal gruppo Aspi, riveste un ruolo di primo piano; proprio per questo, come Amplia abbiamo voluto introdurre su questo cantiere una serie di innovazioni tecnologiche particolarmente interessanti”.
“Questa, come molte altre gallerie sono oggetto di interventi di riqualificazione strutturale profonda, che consentirà di poter estendere la vita utile di questi manufatti, a interventi completati, tra i 50 e i 60 anni (ovviamente con tutte le manutenzioni ordinarie previste in questo arco temporale).
In questa galleria, inoltre, a differenza di molte altre già riqualificate lungo l’asse dell’A26, abbiamo introdotto una nuova tecnologia di getto delle volte che utilizza casseri semoventi particolarmente innovativi”.
Prosegue Onniboni : “In linea generale, ogni intervento di riqualificazione che eseguiamo sui manufatti della rete viene preceduto da una serie di accurate indagini, pensate per determinare con precisione lo stato di degrado del manufatto, che consentono preliminarmente di dare indicazioni quindi sugli interventi da mettere in atto per raggiungere il miglior risultato possibile”.
“Non dimentichiamoci che il nostro obiettivo principale è garantire la massima sicurezza agli utenti dell’autostrada e, quindi, siamo costantemente impegnati nella ricerca di soluzioni tecnologiche innovative che ci consentano di raggiungerlo, e contemporaneamente di eseguire i lavori minor tempo possibile (per diminuire i disagi all’utenza), garantendo comunque un risultato qualitativo di estrema qualità”.
“In questo caso, come in molti altri, abbiamo realizzato un pre-consolidamento radiale preliminare della struttura mediante infissione di tubi in VTR, volto a mettere in sicurezza l’opera, sopratttuto in ottica di mantenere la prestazionalità strutturale del manufatto durante la demolizione controllata del vecchio manto (uno spessore minimale del vecchio involucro viene sempre mantenuto) con tecniche di idrodemolizione (in presenza di armature) o con fresatura meccanica. Successivamente abbiamo provveduto alla posa in opera dello strato di shotcrete di regolarizzazione/protezione (dello spessore massimo di 3 cm)”.
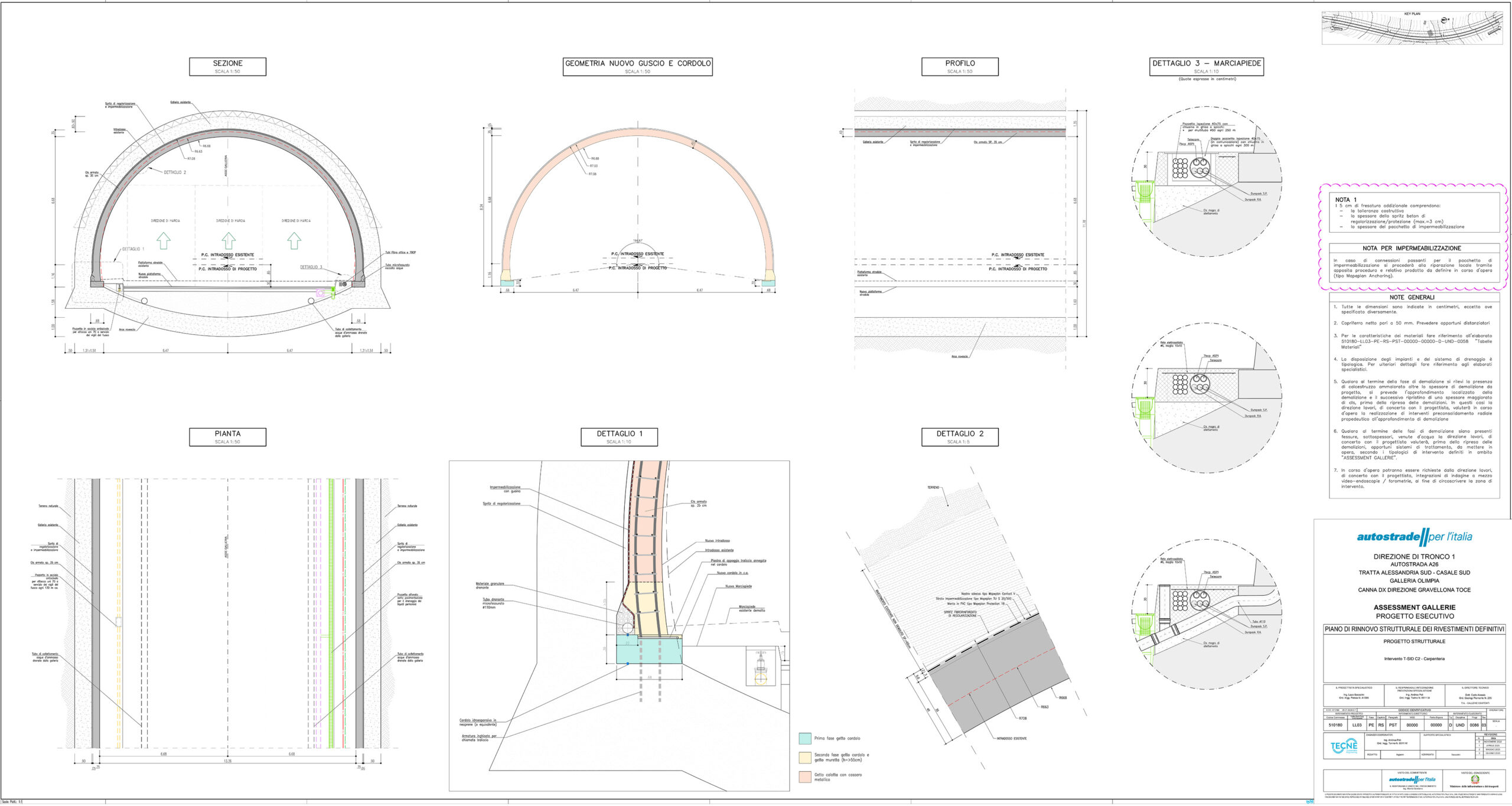
“È importante sottolineare che la nuova galleria ricostruita viene realizzata con tecniche e materiali all’avanguardia e strutture di armatura molto dense, proprio per garantirne la durata nel tempo. Prima di realizzare i getti in calcestruzzo necessari per la ricostruzione, ovviamente, si procede alla stesa di un nuovo manto di impermeabilizzazione, costituito da un impermeabilizzante sintetico in TPO (spessore > 2 mm) accoppiato a doppio strato in TNT: molte di queste gallerie, infatti, all’epoca della loro costruzione non prevedevano opere di impermeabilizzazione, con conseguenti fenomeni di infiltrazione d’acqua che nel tempo hanno degradato materiali e strutture”.
“La galleria Olimpia ha uno sviluppo di circa 850 metri lineari, con tratti limitati agli imbocchi in gallerie artificiale su cui siamo intervenuti con tecniche di idrodemolizione.
Nella galleria naturale, invece, come accennato prima abbiamo alternato, a seconda della situazione prevista dai sondaggi e poi effettivamente rilevata in cantiere, idrodemolizione (dove erano presenti armature) e demolizione meccanica con testa fresante“.
“Per il getto abbiamo utilizzato il carro portaforme semovente fornitoci da Emmerre; si tratta di una tecnologia nuova che, proprio in un progetto più ampio di innovazione tecnologica che stiamo implementando come Amplia, ci consente di sposare due concetti per noi essenziali: un incremento dell’efficienza produttiva (i cantieri così possono concludersi in meno tempo) e un aumento della sicurezza in cantiere. Il carro ci consente grazie ai soli quattro punti appoggio, all’auto livellamento, ai sensori di pressione, alle ruote gommate (il tutto gestito da un plc dedicato) di avanzare, armare e disarmare in pochissimo tempo”.
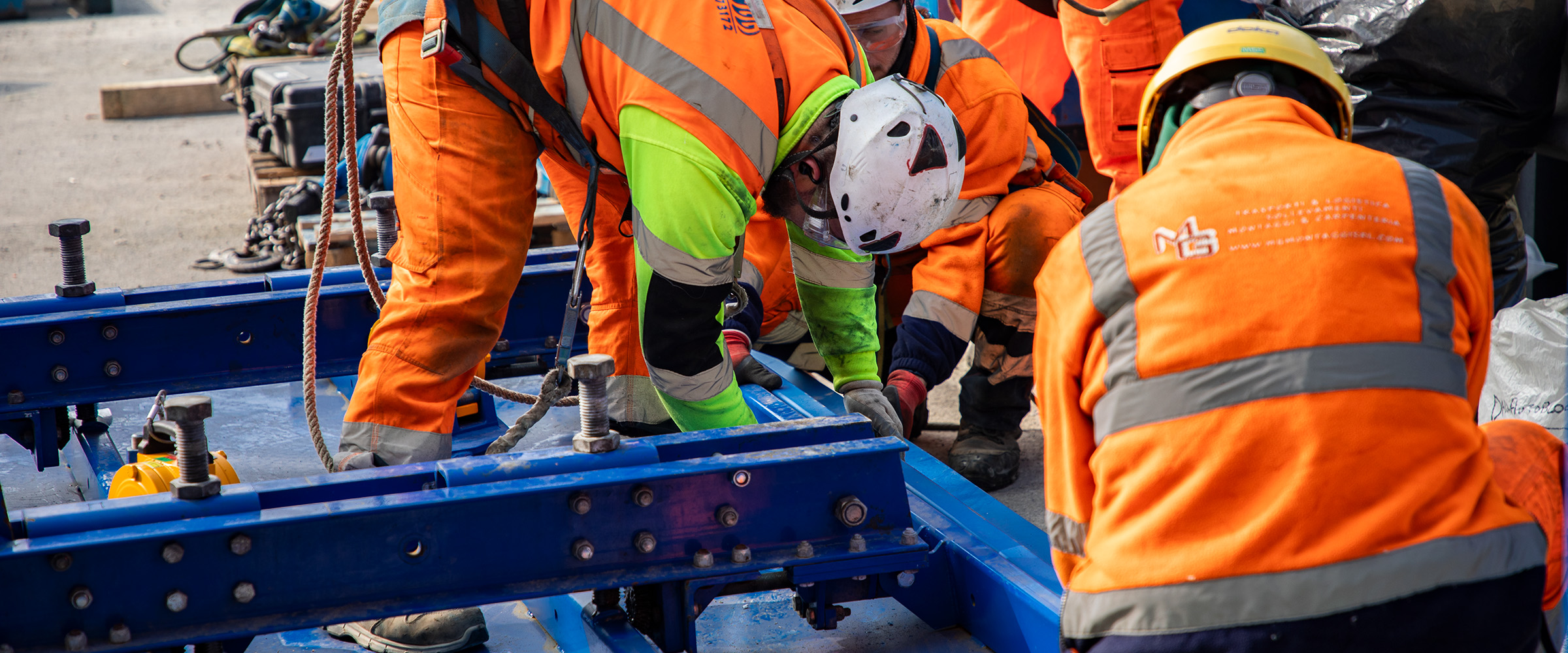
“Quest’ultimo aspetto, come Amplia, è per noi fondamentale: da questo punto di vista, con un ottica strategica di ampio respiro, che poi si declina su ogni singolo cantiere, stiamo investendo davvero molte risorse, tecniche e finanziarie, per rendere il lavoro dei nostri collaboratori più sicuro.Dalle prime esperienze posso già dire che, inoltre, la qualità del manufatto gettato con questo tipo di cassero, è decisamente migliore rispetto ad altri sistemi più tradizionali che abbiamo sperimentato in passato”.
Continua Onniboni: “Da un punto di vista della sequenza operativa, la costruzione del nuovo manufattoparte dalla realizzazione dei cordoli di appoggio in c.a. che si vanno ad innestare sull’arco rovescio della galleria originale; da questi cordoli partono le armature strutturali a traliccio (che vengono preallestite all’esterno della galleria). Si procede quindi al getto delle murette laterali su cui andrà in appoggio il cassero con il quale verranno realizzati i vari conci (della lunghezza di sei metri cadauno) della volta della galleria”.
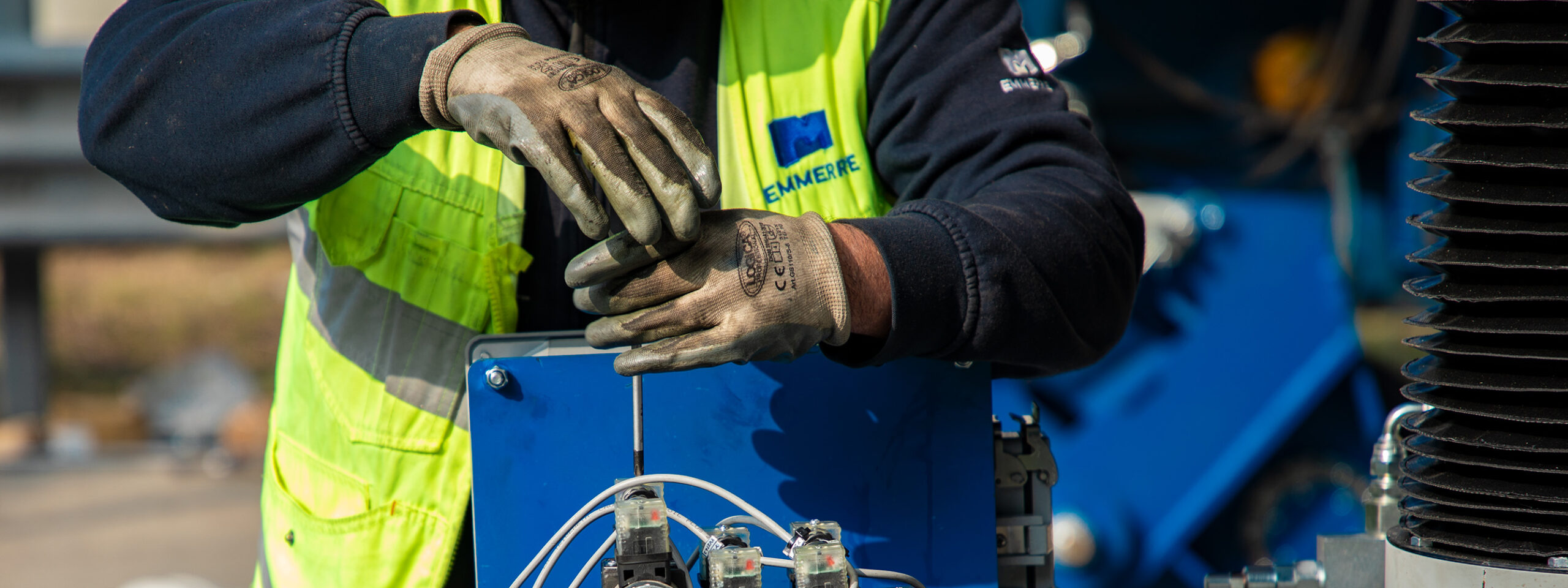
“In questo cantiere abbiamo deciso di utilizzare contemporaneamente tre casseri Emmerre, che lavorano con getti sfalsati temporalmente su tratti di galleria differenti in modo da utilizzare in maniera efficiente la capacità produttiva degli impianti di produzione di calcestruzzo a cui ci appoggiamo (mentre si getta il primo cassero, il secondo ha il getto in fase di maturazione e il terzo è nella fase di spostamento): ricordo che il calcestruzzo ci viene consegnato con autobetoniere che circolano sul tracciato autostradale e quindi sono soggette a eventuali problemi derivanti dal traffico stesso”.
Conclude Onniboni : ”Il grande vantaggio di questo cassero è che, una volta completato il getto, non sono necessarie altre lavorazioni (obbligatorie per tecnologie alternative, come ad esempio lo spritbeton fibrorinforzato che richiede operazioni di rasatura e lisciatura) per migliorare la superficie a vista dei manufatti realizzati. Si tratta di un considerevole incremento dell’efficienza produttiva che ci consente, lo ripeto, di ridurre l’impatto dei cantieri sul traffico autostradale”.
“I casseri, inoltre, consentono di ridurre il personale impegnato in gallerie e aumentano quindi la sicurezza intrinseca del cantiere stesso, un altro aspetto fondamentale per Amplia”.
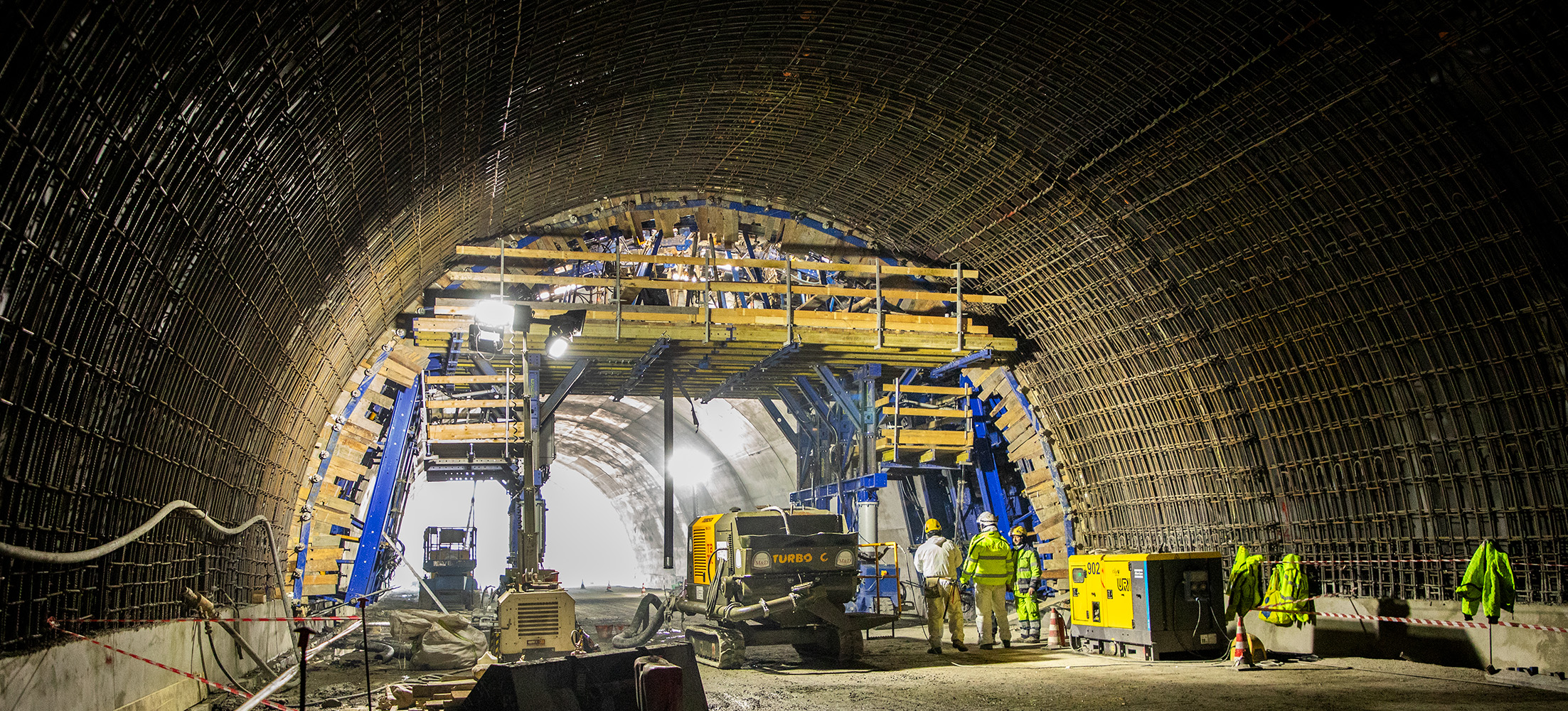
Triplo arco
Delle caratteristiche tecniche del carro porta forme Volto con sistema MR4.0 parliamo con Roberto Roberto , diretto tecnico e fondatore, con Michele Mancini , di Emmerre: “É la prima volta che forniamo su un unico cantiere ben tre carri con sistema Volto e soluzione semovente (che abbiamo brevettato) MR4.0. Con Amplia, che ci ha chiesto i tre carri a noleggio, comprensivi di assistenza tecnica e montaggio in cantiere, abbiamo stabilità che l’utilizzo di tre casseri in contemporanea lungo la galleria avrebbe potuto aumentare decisamente la produttività, incrementando contemporaneamente la sicurezza operativa rispetto ad altre soluzioni tradizionali”.
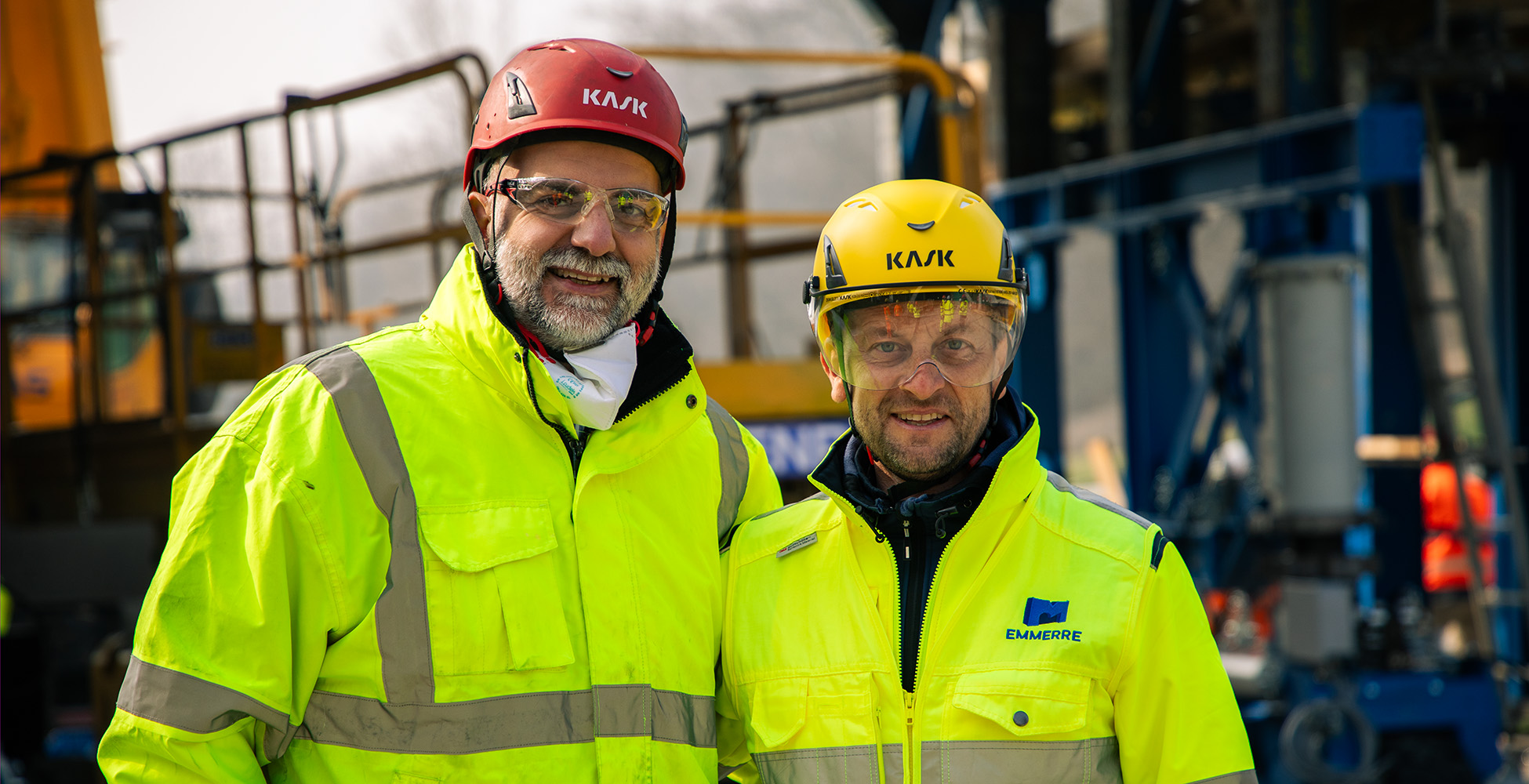
Prosegue Roberto: “In questo cantiere vediamo al lavoro tre nostri brevetti: il sistema di casseratura a raggio variabile Volto, che ci consente di realizzare qualsiasi tipo di galleria con raggi costanti o policentrici a partire da un raggio di curvatura di 1,70 m ed effettuare portali, che determinano la lunghezza della cassaforma, con multipli di 3,00 m, e il nostro nuovo portale semovente 4.0”.
“MR 4.0 è un innovativo sistema di carro porta forme motorizzato, strutturato su quattro appoggi principali (ognuno servito da due ruote in gomma basculanti che si sollevano durante la fase di getto) che può superare pendenze fino al 18% (quando tutte e quattro le ruote siano motorizzate)”.
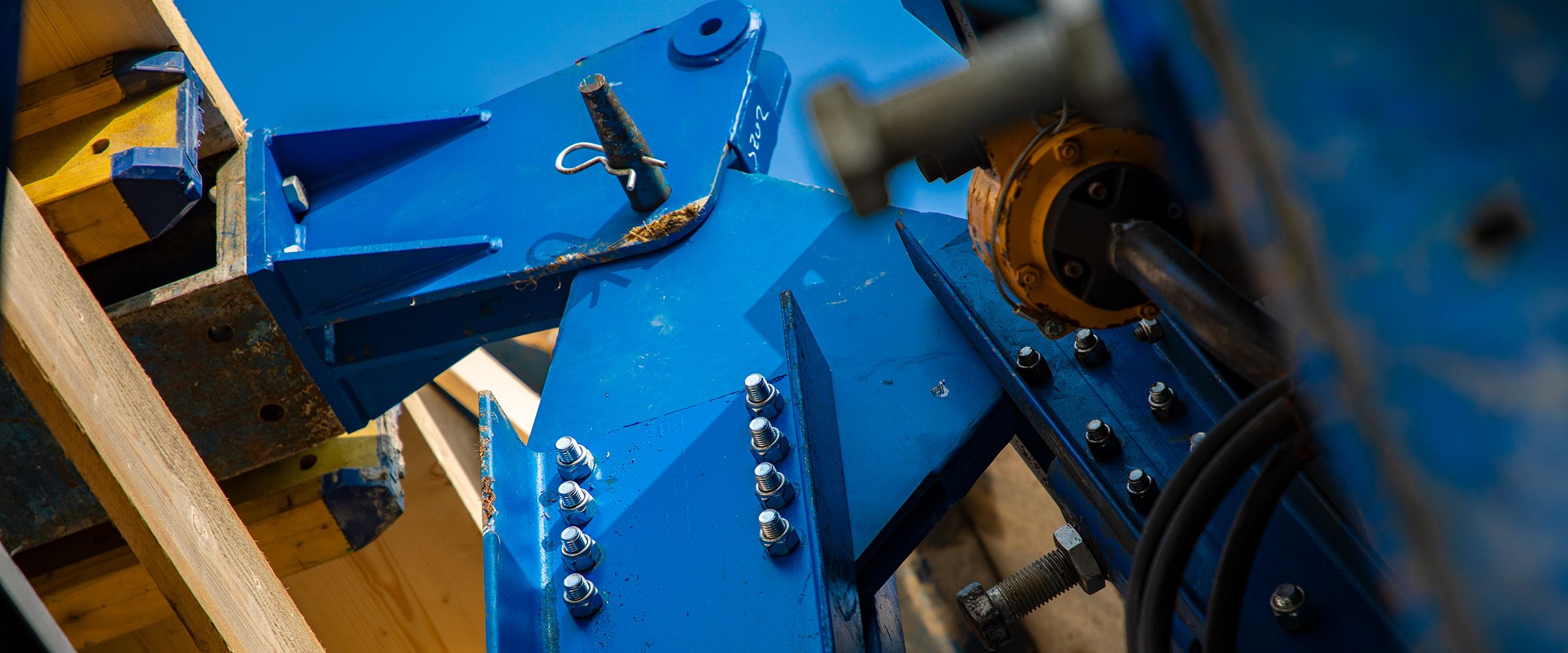
“Tanti i vantaggi di questa abbinata di sistemi, non solo a livello di produttività, ma anche e soprattutto di sicurezza: il nuovo carro MR 4.0 è caratterizzato da un notevole livello di automazione che consente all’operatore di gestirne la movimentazione e l’intero settaggio (anche la messa in quota e l’apertura e chiusura del manto in acciaio Volto) da un radiocomando, senza dover essere a bordo dell’attrezzatura, con importanti vantaggi dal punto di vista della sicurezza sul lavoro. Abbiamo, inoltre, messo a punto un sistema di livellamento laser automatico che utilizza due bolle laser all’interno della struttura, consentendo di mantenere la livellazione trasversale durante tutto lo spostamento”.
“Con il nostro sistema, la cassaforma viene armata e disarmata, azionando solo i quattro pistoni del portale (ognuno in grado di sviluppare 2000 kN), ognuno monitorato con una propria cella di carico; tutte le sollecitazioni vengono scaricate attraverso questi quattro punti e non sono presenti scatole a cuneo (tra l’altro questo aspetto rende i cicli di getto molto più veloci ed efficienti)“.
Conclude Roberto: “Questo consente, torno a ripeterlo perché per noi si tratta di fattori fondamentali, maggiore sicurezza, meno lavorazioni e quindi maggior velocità delle operazioni. Inoltre, grazie ai sensori e al PLC dedicato, i pistoni sono in grado, una volta raggiunta la quota desiderata, di auto livellare autonomamente la cassaforma oltre a segnalare, in fase di getto, eventuali carichi eccessivi sulla struttura. E anche in questo caso abbiamo un importante impatto sulla sicurezza operativa di cantiere”.